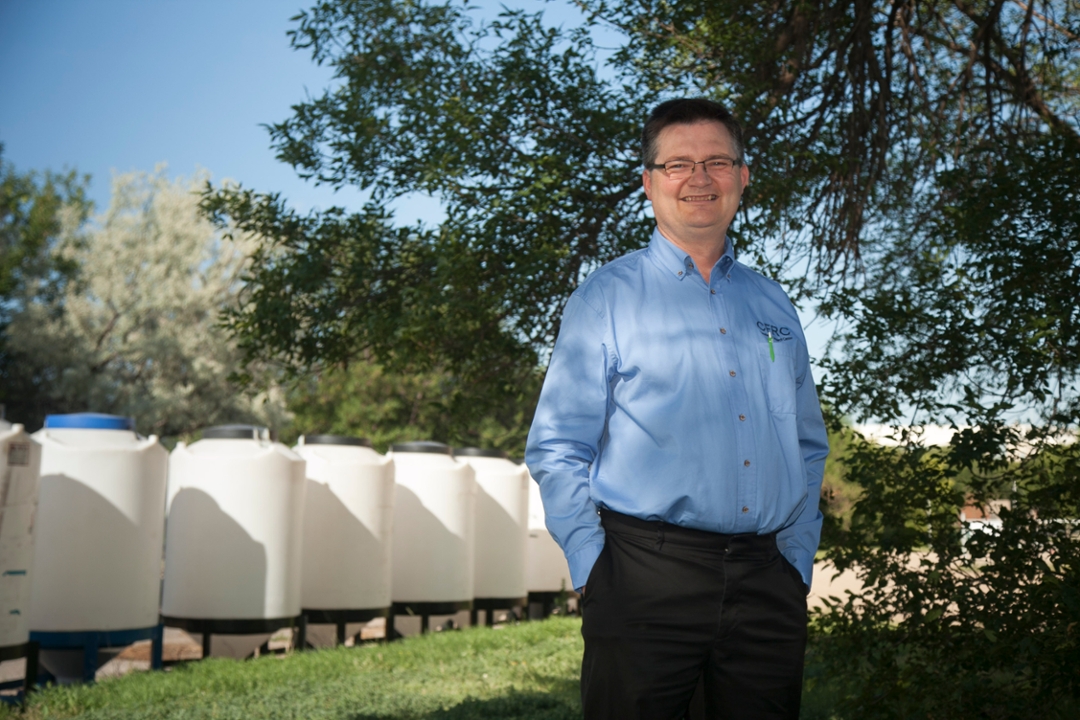
More From Less
Why North Battleford is the place to be in the (surprisingly big) world of livestock feed
By Glenn Cheater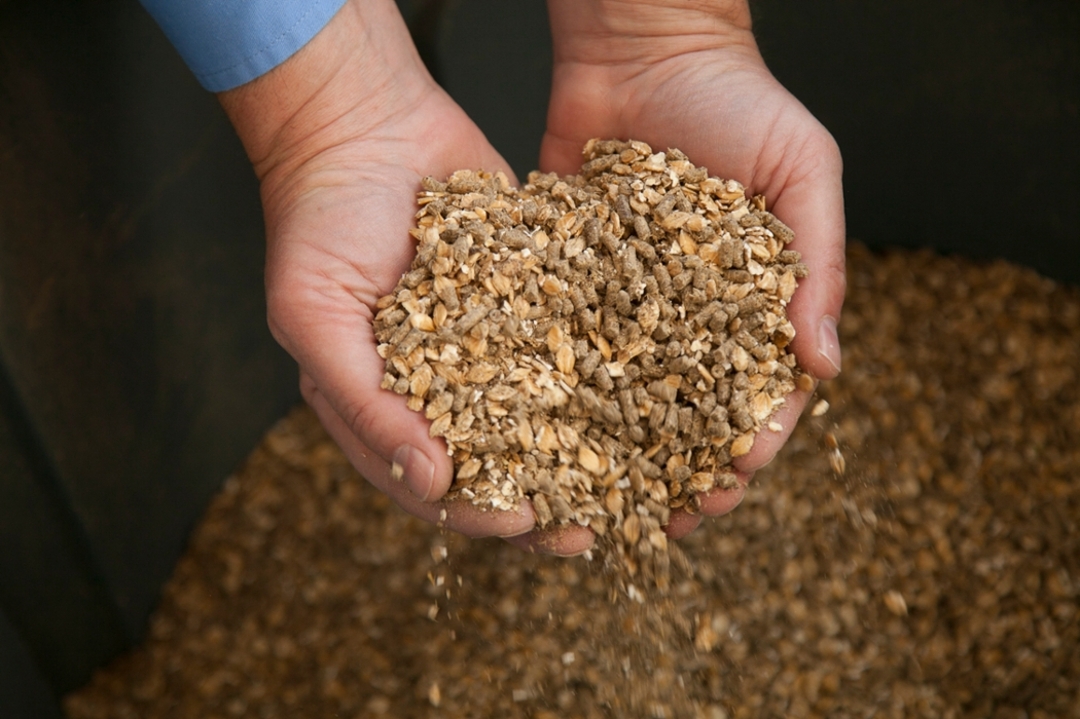
It’s one of the biggest resource enterprises on the planet, but most people aren’t aware of it. “We often overlook just how much of agricultural production goes into the feed industry,” said Rex Newkirk. “Last year, we were just shy of one billion tonnes of feed manufactured in the world. In Canada, probably around 35 per cent of our total agricultural production goes into the feed industry.”
Those sorts of stats have become, so to speak, fodder for meat-is-bad-for-the-planet critics, who argue that farmland would be better used for feeding people, not livestock.
But if you paid a visit to Newkirk’s pride and joy — the Canadian Feed Research Centre in North Battleford—you’d see an entirely different side of the story.
“One of the other things that’s not well understood is that we use a lot of byproducts to make feed,” said Newkirk, associate professor and Ministry of Agriculture Endowed Research Chair of Feed Processing Technology.
“We not only use a lot of off-grade grain, we also divert a lot of products from the landfill that people don’t eat. The feed industry does a lot of that—turning waste ingredients into high-quality products.”
Both of those areas are a major focus of his work.
Newkirk sounds like a kid in a candy store as he describes various projects he has on the go. “I grew up on a farm welding, machining, and banging on things with a hammer—I like making things work better,” said the 49-year-old. “Here I get to do applied research on getting more val-ue for our crops. That’s always been my driving force. What can we do to get more out of our resources?”
The three-year-old research centre looks pretty much like any feed mill (which it was before be-ing extensively retrofitted). But inside, Newkirk and his team of researchers and technicians are busy with a host of projects that attract visitors from around the world. There are three pro-cessing lines—from one able to produce 20-kilogram batches to a 20-tonnes-per-hour commercial line that his team gets to use in between production runs by a major feed processor (whose lease helps cover the facility’s costs).
But unlike a regular feed mill, Newkirk and his team get to play—using advanced technology to pioneer new feeds and processes that industry can adopt.
Take, for example, their research into grain damaged by a fungus called fusarium graminearum, which produces something called vomitoxin. Humans and livestock can only tolerate minute amounts, but fusarium is widespread. In 2016, roughly 80 per cent of Saskatchewan and Manito-ba cereal crops were infected, costing farmers an estimated $1 billion.
A Swedish machine using technology called “near infrared transmission” can scan and sort out individual infected kernels. The research centre obtained one of the first of these machines, worked out the issues in scaling up to commercial applications, and then invited industry players to come and see it in action.
“In a normal feed mill, it would be difficult to mess around with that, but in a research centre like this, we can do that kind of thing,” said Newkirk, noting some Prairie feed mills are now in-stalling the machines.
He’s equally excited by his new toy—and who wouldn’t love a “steam explosion” machine? “It won’t be quite as dramatic as it sounds, but I still think it’s a really cool thing,” he said with a laugh.
The device breaks down cellulose, the fibrous polymer produced by plants to give strength to their stalks and other structural bits. Thanks to multiple stomachs and the bacteria that live in them, ruminants like cows can break down some of this cellulose. But much of it passes right through them. Making cellulose more digestible would be a double win—better feed efficiency and less manure.
Steam explosion does that by briefly using high pressure and temperature to first melt lignin (the “glue” that binds the fibres together) and push moisture into the fibres. When the pressure and temperature are quickly reduced, the moisture turns to steam and “explodes” (albeit quietly) the fibrous mass.
The technology has been embraced by the ethanol sector, where the holy grail is to make cellulose fermentable so it can be economically turned into fuel. Doing that in large volumes has proven too expensive so far, but Newkirk’s idea is that the technique could be adapted economically for feed production.
“I don’t want to go to the extremes you need to make it fermentable. What I want to know is: what’s the minimum I can do to get the maximum amount of nutrients? And can I scale it up?” He’s taking a similar practical approach to another technology, also using near infrared, to meas-ure ingredients in feed as it’s being made. Feed makers always err on the safe side—it’s better to have too much protein or energy than too little. Farmers do the same thing, and the result is wast-ed nutrients going out the back end of an animal.
That’s something that Newkirk—who grew up on a cattle ranch near Maple Creek, Sask.—would like to change.
“I think my approach comes from that practical side of farming: how do we feed these cows more efficiently at the least cost?”
It’s a quest he’s been on for most of his adult life, following a PhD on utilizing canola meal with a 12-year stint at the Canadian International Grains Institute, where he promoted feed grains to buyers from around the world. He now specializes in poultry feed.
His new position fuses all those things together—researching innovative ideas, making them work in the real world, and then inviting in industry players and saying, “Take a look, here’s how it works,” he said.
“The industry has a lot of smart people and while they work very hard, I see a lot more potential. For me, this is a very exciting place to be.”